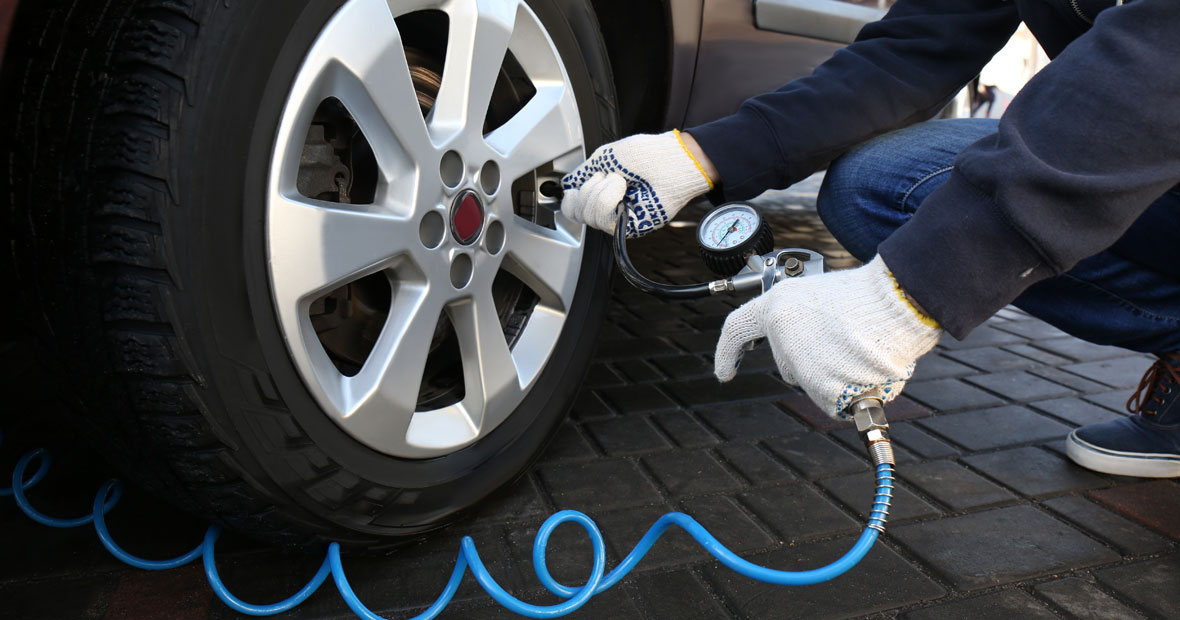
L'outillage pneumatique, composé de divers instruments, fonctionne à son maximum sous une pression d'air spécifique. Une pression de 6,3 bar (90 psi) en dynamique favorise un rendement optimal. Cependant, une baisse de pression peut entraîner un déclin de performance, impactant la productivité. La plage de pression recommandée pour maintenir l'efficacité de l'air comprimé varie de 5,5 à 7,6 kg/cm2 (80 à 110 psi). Une pression d'air inadéquate peut causer des problèmes allant d'une simple baisse de rendement à de graves problèmes d'efficacité. Le choix d'un compresseur adéquat est donc nécessaire.
Pression d'air requise pour le fonctionnement optimal des outils pneumatiques
Dans le choix des outils pneumatiques, la pression d'air est un paramètre élémentaire pour un fonctionnement optimal. Ces outils, incluant cloueuses, perceuses et ponceuses, ont tous un besoin spécifique en pression d'air. Des études réalisées par des instituts de recherche ont démontré l'importance de la régulation de cette pression pour prolonger la durée de vie des outils pneumatiques. Un dysfonctionnement peut résulter d'une pression d'air trop élevée ou insuffisante. Le site kstools.fr mentionne la pression recommandée pour chaque outillage.
Pression de 6,3 bar (90 psi) en dynamique
Une pression de 6,3 bar (90 psi) en dynamique est considérée comme relativement élevée et nécessite des équipements robustes pour supporter ces conditions. Cette pression est couramment utilisée dans les systèmes hydrauliques et pneumatiques sollicités, comme ceux des industries lourdes, de la construction ou des freins de véhicules lourds. À ces niveaux de pression dynamique, les forces exercées sur les composants mécaniques et les tuyauteries sont importantes, ce qui requiert des matériaux résistants et des conceptions renforcées pour éviter les fuites et les défaillances prématurées. Des dispositifs de sécurité et de contrôle sophistiqués sont également nécessaire pour gérer les fluctuations de pression et prévenir les risques.
Perte de performance avec une pression plus faible
Lorsque la pression d'un système dynamique est inférieure à la valeur nominale requise, cela peut entraîner une perte de performances. Par exemple, dans un système hydraulique fonctionnant à une pression trop basse, la force de poussée générée sera réduite, ce qui peut affecter la puissance et l'efficacité des actionneurs. De même, dans un système pneumatique, une pression insuffisante limitera le débit d'air et réduira la capacité des vérins ou des outils à développer leur pleine puissance. Cette baisse de pression peut également compromettre le fonctionnement optimal des composants, augmenter les risques de cavitation ou de coups de bélier, et accélérer l'usure prématurée du système. Il faut maintenir la pression adéquate pour garantir des performances optimales, une efficacité énergétique maximale et une durée de vie prolongée des équipements.
Plage de pression recommandée : l'air comprimé dans une plage de 5,5 à 7,6 kg/cm2 (80 à 110 psi)
Pour les systèmes utilisant de l'air comprimé, la plage de pression recommandée se situe généralement entre 5,5 et 7,6 kg/cm2 (80 à 110 psi). Cette fourchette permet un équilibre optimal entre la puissance fournie et la sécurité d'utilisation. Une pression inférieure à 5,5 kg/cm2 peut ne pas être suffisante pour alimenter correctement les outils et les actionneurs pneumatiques, entraînant une perte d'efficacité. À l'inverse, dépasser 7,6 kg/cm2 augmente les risques de fuites, de défaillances prématurées des composants et de situations dangereuses en cas de rupture. La plage de 80 à 110 psi permet donc d'exploiter pleinement les capacités des équipements pneumatiques tout en respectant les limites de sécurité établies par les normes industrielles. Un réglage précis et un suivi régulier de la pression sont nécessaire pour maintenir un fonctionnement optimal et fiable du système.
Conséquences d'une pression d'air inadéquate : manque de pression d'air, une baisse de performance et de productivité des outils pneumatiques
Un manque de pression d'air ou une pression inadéquate dans un système pneumatique peut avoir des conséquences néfastes sur les performances et la productivité des outils et équipements alimentés par l'air comprimé. Lorsque la pression est trop faible, les outils pneumatiques tels que les clés à chocs, les perceuses ou les pistolets à river ne peuvent pas développer leur pleine puissance, ce qui se traduit par une baisse d'efficacité et un ralentissement des opérations. De plus, un déficit de pression peut provoquer des dysfonctionnements, une usure prématurée des composants internes et une consommation d'air excessive, entraînant des coûts d'exploitation plus élevés.
À l'inverse, une surpression excessive peut également endommager les outils et représenter un risque pour la sécurité des opérateurs. Il faut maintenir une pression d'air appropriée, conforme aux spécifications des équipements, afin d'optimiser leur rendement, leur durabilité et leur fiabilité. Un système d'alimentation en air comprimé correctement dimensionné, régulièrement entretenu et doté de régulateurs de pression précis est la clé pour éviter ces problèmes de performance et de productivité liés à une pression d'air inadéquate.
Choix du compresseur adapté en tenant compte de la pression d'air requise par les outils utilisés
Le choix d'un compresseur à air approprié est nécessaire pour répondre aux besoins en pression d'air des outils et équipements pneumatiques utilisés. Il faut sélectionner un modèle capable de fournir une pression d'air suffisante pour alimenter correctement les outils, sans compromettre leurs performances ni leur durabilité. Une pression inadéquate peut entraîner une baisse d'efficacité, une usure prématurée et une consommation d'énergie excessive.
Lors du choix d'un compresseur à air, il est nécessaire de tenir compte de la pression maximale requise par les outils les plus exigeants, ainsi que du débit d'air nécessaire pour un fonctionnement simultané de plusieurs équipements. Les spécifications techniques des fabricants d'outils doivent être soigneusement examinées pour déterminer les besoins en pression et en débit d'air. Un compresseur surdimensionné peut être coûteux et énergivore, tandis qu'un modèle sous-dimensionné ne pourra pas répondre aux exigences de l'application.
Il est également recommandé de prévoir une marge de sécurité supplémentaire pour compenser les pertes de pression dans les tuyaux et les raccords, ainsi que pour anticiper les besoins futurs en cas d'ajout d'outils ou d'équipements supplémentaires. Un choix judicieux du compresseur à air garantira des performances optimales, une durabilité accrue et une efficacité énergétique maximale.